Ball Mill
In the pharmaceuticals field, a ball mill is primarily used as a grinder and mixer to combine various drugs with a fine powder. It also ensures the thorough mixing of all of the components.
One of the main goals is the size reduction of the subjected materials.
The mill consists of a hollow cylinder with an attached pipe at a certain angle, usually 60°. Inside the cylinder, are spherical bodies, grinding medium, that represent the ‘balls.’ This cylinder rotates about its axis, thus moving the contents in it. The balls in the cylinder are responsible for mixing and coating. The materials are fed into the cylinder through an attached pipe. Another pipe attached at the bottom at an angle of 30° removes the processed materials out of the rolling mill. The structure and mechanism ensure solid particles are reduced in size by the impact of balls and the walls of the rotating cylinder.
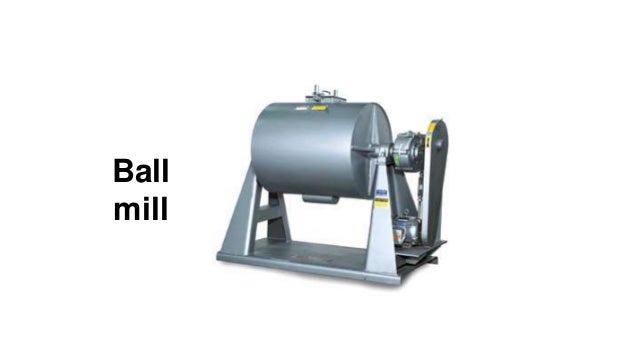
Grinding in a ball mill depends on a certain number of properties:
- The size of the grinding media should be larger than the size of the solids that need grinding.
- The grinding media should be durable and should not get disintegrated or broken into smaller pieces while grinding. However, it should also not wear out the tumbler.
- Flammable products such as steel tend to become explosive on the powdered form. Hence, utmost care should be taken while grinding steel, not to induce a spark. In such cases, prefer ceramic grinding media.
- Note the color of the material and grinding media, where the color of the end ground particles is necessary.
- Avoid Corrosive reactions.
- The grinding chamber can also be filled with an inert gas to reduce the risk of oxidation and explosive reactions.
Ball mill has several advantages, including
- Lower installation cost,
- Comparatively low prices of grinding media,
- Compatibility for both; batch and continuous grinding,
- Compatibility for open and closed grinding environments, and
- It can be used for all materials with varying degrees of hardness.
Hammer Mill

As the name suggests, a hammer mill is a crushing mill that employs hammers to break/crush materials into smaller pieces. This type of crushing is employed in a wide range of fields right from agriculture to a pharmacy to geology to automobiles. Because of its versatility, it is usually the most commonly preferred method of crushing materials.
The hammer mill operates by crushing the fed materials against the swinging or rotating hammers placed inside the steel drum. The orientation of this drum can either be horizontal or vertical, and the hammers swing across the axis from a cross-like motion, or they can rotate, thereby crushing the feeding. The material is fed through a hopper, and a grate is attached to the edge of the steel drum to determine the grain size of the final crushed end-product.
The most commonly used application of such a process is seen in a flour mill, where wheat is fed in from one side, the grains get smashed across the walls of the steel drum and are pounded by these hammers. The rotation or the movement of these hammers keeps the grain moving and simultaneously crushing it at the same time. After crushing to the required size, it gets filtered out of the grate and falls into a collection pile.
There are two types of hammer mill crushers – “up running,” which use grates or perforated screens to separate the crushed material. Such machinery usually has an adjustable speed to control the quality of the crushed material and to control the wear of the drum. Second, are the “Down running” machines that are suitable for fibrous materials as high shearing grinding takes place.
Fluid Energy Mill

A fluid energy mill is typically employed to crush particles to a tiny, sub-sieve size (< 10µ). This type of crushing is employed when fine powders are needed, and the system needs to be energy efficient. It is said to be a super effect for crushing heat-sensitive materials as the fluid in the fluid energy mill can dissipate much of the heat generated during the grinding process.
The working of the fluid-energy mill uses one or more fluid streams with high velocity, one of which contains the material to be ground, and another stream which may carry another partially treated material or the grinding media. Grinding happens when these streams collide with each other, and the particles suspended in them are subjected to crushing due to the collision instead of them getting ground due to collision with the walls of the mill.
Grinding using such a mechanism has several advantages: rapid cooling due to heat dissipation by the flowing streams, high purity and a lower risk of contamination due to a concealed environment of the material suspended in the fluid medium, the machinery is relatively compact and can be used in a continuous mode of operation are to name a few.
Disintegrator
A disintegrator mill is used for crushing and grinding hard, solid particles into a powder. The coarseness of the product depends on the application of the material. The disintegrator mill is one of the most robust forms of grinding, as is usually not preferred for delicate materials.
The disintegrator mill grinds and breaks down the solid material by passing it through a series of crushers, which become fine at every succeeding level, this regulated and filtered grinding ensures a fine powder. The machinery of this kind if the mill is straightforward. The big, solid chunks are fed into the crushers from a generally broad opening where they are broken down into smaller pieces by rotating crushers, as they are broken into smaller pieces these pieces pass through the gaps between these crushers to the second level where they are subjected to further crushing. This process is repeated until is the desired result is obtained.
Although the mill has cheaper set-up and operating costs, it is susceptible to the addition of impurities and can also give unevenly crushed materials. Hence, this method of grinding is employed when big chunks need to be broken down into a smaller, more coarse powder, which can later be subjected to a more delicate and more filtered grinding.